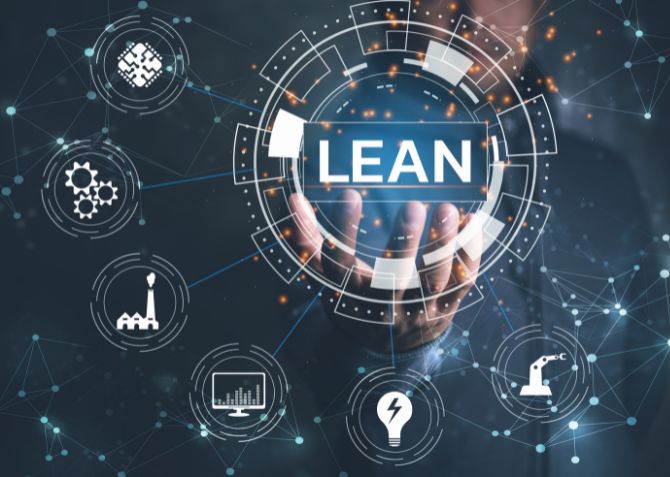
Recent years have seen a rise in popularity of lean manufacturing, with businesses looking to enhance their production processes and limit redundancy. Lean manufacturing principles emphasize the detection and removal of activities that do not contribute to the final product, resulting in decreased expenses and augmented productivity.
In this blog post, we delve into the core idea behind lean manufacturing, as well as its main principles, benefits, and the challenges faced by companies implementing these strategies.
Furthermore, we will explore how logistics companies can adopt lean thinking to streamline their operations when transporting merchandise cross-border.
Table of Contents:
- What is Lean Manufacturing?
- Benefits of Lean Manufacturing
- Challenges of Applying Lean Manufacturing Principles
- Logistics Companies and Lean Manufacturing
- Conclusion
- FAQs Regarding Lean Manufacturing Principles
What is Lean Manufacturing?
Lean manufacturing is a set of principles and practices developed to maximize efficiency in the production process. The concept was originated in Japan in the 1950s through the Toyota Production System. One of the most popular books covering the topic is “The Toyota Way: 14 Management Principles from the World’s Greatest Manufacturer” by Jeffrey K. Liker. The main concept focuses on eliminating waste, streamlining processes, and increasing quality while reducing costs.
The aim of lean manufacturing is to provide customers with what they need at the lowest possible cost, while also enhancing quality and cutting costs. Lean manufacturing involves an ongoing cycle of improvement where new solutions are constantly sought out and implemented, in order to further reduce waste and improve efficiency.
Lean manufacturing started in Japan with Toyota company in the 1950s.
The core principle behind lean manufacturing is “value” – creating products or services that customers find valuable, without producing any excess inventory or wasting resources such as time, money, materials, energy, etc. To achieve this goal, companies must identify areas where waste can be eliminated from their production processes; this could include anything from reducing lead times to improving communication between departments or optimizing machine utilization rates. Once these areas have been identified, it’s important to implement changes quickly so that improvements can be seen right away.
Continuous improvement (CI) is a key practice within lean manufacturing, requiring setting goals for improvement and working towards them through small incremental steps over time. This approach allows for quick adjustments to be made if needed, based on how well the changes play out in reality, rather than just theory.
Close oversight of outcomes must be kept up to guarantee progress, so any issues can be quickly addressed before they become more serious.
Lean production is a system that concentrates on cutting down redundancy and augmenting efficacy. By implementing lean principles, businesses can improve their bottom line while also enhancing customer satisfaction.
Benefits of Lean Manufacturing
Lean production is a system of approaches and techniques that have been employed to refine the fabrication procedure for years. As we have already covered, the core idea is to reduce waste, minimize costs, and increase efficiency. This can be done by eliminating unnecessary steps in the production process and focusing on the value-added activities that will bring products from concept to completion faster.
One of the biggest benefits of implementing lean principles into your production process is cost savings. By reducing waste throughout your operation, you can lower overhead expenses while still producing quality goods at an accelerated rate. Additionally, by cutting down on time spent waiting for parts or materials needed for production, you can get more out of every hour worked without having to sacrifice quality standards or customer satisfaction levels.
Lean manufacturing principles are based on maximizing efficiency and minimizing waste, which can lead to cost savings.
Another advantage of using lean methods in your manufacturing processes is improved customer service. By streamlining operations and removing delays due to wasteful practices such as overproduction or excess inventory management, customers receive their orders faster. This leads to increased satisfaction levels with their overall experience with your company’s product line or services offered.
Additionally, this type of system helps ensure accurate delivery times, so customers know exactly when to expect their order instead of having it arrive late due to inefficient processes within your organization’s supply chain network.
The benefits of lean manufacturing can help businesses improve their efficiency and profitability, making it an attractive option for many. Despite its advantages, implementing lean manufacturing principles can be difficult and requires addressing certain challenges.
Challenges of applying Lean Manufacturing Principles
Lean manufacturing has become a popular approach for streamlining production and cutting costs, but it is not without its potential difficulties that businesses should be aware of before making the transition. The most common challenges include:
1. Resistance to Change
Many employees may be resistant to changes in the traditional workflow, which may lead to delays or even complete failure of the project. It’s important for companies to provide training and education about lean principles, so that everyone is on board with the new process.
Training on lean principles helps overcome employee resistance, avoiding project delays.
2. Quality Control Issues
In order for any lean implementation strategy to work properly, it needs an effective quality control system in place from start to finish. Lack of proper oversight can lead to errors more easily as products move through different stages of production faster than before, due to streamlined processes.
3. Lack of Resources
Lean initiatives require resources such as personnel, materials, and equipment that may not always be available when needed or cost-effective enough for budget constraints. Companies should consider their current resources when deciding if they have enough capacity for a successful transition into lean operations management methods like Just In Time (JIT).
The challenges of Lean Manufacturing can be daunting, but with the right logistics partner and proper implementation strategies, businesses can reap the rewards of improved efficiency. Logistics companies are an integral part of successful lean manufacturing initiatives; they provide valuable insight into cross-border operations that help streamline processes and reduce costs.
Logistics Companies and Lean Manufacturing
One key element of lean manufacturing is just-in-time (JIT) inventory management. This method involves only ordering what is needed when it is needed, rather than stockpiling supplies or materials in advance. JIT inventory helps reduce storage costs by ensuring that nothing sits idle for too long before being used. It also eliminates overproduction, as items are ordered only when they’re actually required for production or delivery purposes.
For cross-border transportation operations like those we offer at the ILS Company, this means having the right amount of cargo ready at all times. This way, you can ensure timely deliveries without excessive delays due to inadequate supply levels or unnecessary surpluses of goods waiting to be shipped out.
Lean manufacturing uses JIT inventory, reducing waste and excess inventory.
Process mapping enables organizations to identify any redundant tasks or areas where processes can be streamlined, thus allowing them to optimize resources and timelines for maximum efficiency gains. This could involve activities such as loading/unloading cargo containers, packing/unpacking shipments, scheduling pickups/deliveries with carriers, etc. These activities are often spread across multiple departments within an organization. By doing so, logistics companies can reduce the amount of time and effort wasted on unnecessary activities while meeting customer demands faster with fewer errors along the way – all without breaking a sweat.
Logistics companies that understand and apply lean manufacturing principles can reduce costs, increase efficiency, and create a competitive advantage in the global market. With this knowledge as our foundation, we now turn to consider how these concepts can be applied every day.
Conclusion
Lean manufacturing is an effective tool for streamlining logistics operations. Lean manufacturing provides businesses with the possibility to cut expenses, optimize effectiveness, and enhance customer satisfaction. However, it can be difficult to implement and requires careful planning. Companies must consider their unique needs and capabilities when implementing lean principles in order to maximize success.
Logistics companies that specialize in cross-border transportation can help businesses navigate the challenges of applying lean manufacturing techniques across international borders.
At the ILS Company, we have specialized expertise which allows us to provide tailored solutions for customers’ individual needs. By utilizing our experience, we can help your company reduce costs associated with shipping goods between Mexico and USA while also increasing efficiency within your supply chain management processes.
FAQs Regarding Lean Manufacturing Principles
1. How does Lean Manufacturing Eliminate Waste?
Lean manufacturing focuses on eliminating waste, such as unnecessary steps or materials in the production process, to maximize efficiency and reduce costs.
2. How does Lean Manufacturing Maximize Value?
Lean manufacturing seeks to create maximum value for customers by producing only what is needed when it’s needed at a quality level that meets customer expectations.
3. How does Lean Manufacturing Pursue Perfection?
The goal of lean manufacturing is continuous improvement with an emphasis on perfection—seeking out better ways of doing things while also striving for zero defects in products and processes.
4. Does Lean Manufacturing Respect People?
People are seen as the most important resource in any organization; respect for people includes providing training opportunities and creating a culture of collaboration among employees, suppliers, and customers.
5. How does Lean Manufacturing Create a Flow?
Creating smooth flow throughout the entire production system allows work to move quickly from one step to another without delays or interruptions that can lead to wasted time or resources.