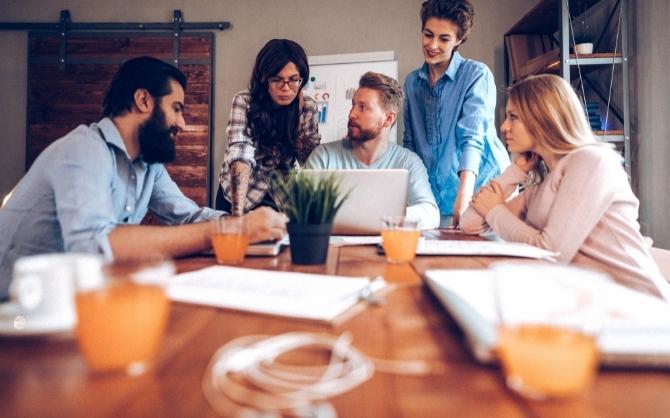
Continuous improvement plays a fundamental role within companies in order to achieve operational excellence. Although it may seem an overwhelming process, the reality is that its correct execution can bring a positive change to your business.
But what is continuous improvement? What makes a good continuous improvement program? Who are the actors in such programs? And what are its main components? These are some of the most common questions that can be asked when implementing a continuous improvement program. Let’s look into it and try to answer them in this post.
What is continuous improvement?
To make it short, continuous improvement focuses on time optimization and cost reduction. These are the two most important actions that can help a company find better performance. It is based on identifying the key processes of a company’s operations and finding areas for improvement. This will lead to strategies to make each process more efficient.
A company that knows its specific pain points and is willing to work on the lessons learned by correcting old habits, is more likely to manage its competitive advantages and position itself in a leading position.
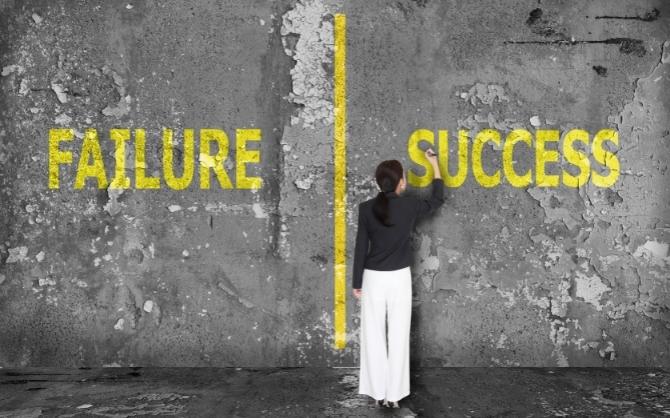
Identifying areas for improvement within a company can lead to success.
What is a continuous improvement program?
Continuous improvement programs are based on joint actions looking for operational optimization; however, this does not mean that any action has a place in them. The search for incremental improvements within companies places in the foreground the ability of a business to evolve, finding better processes that adapt to its needs and allow it to enhance both its competitive advantage as well as its performance.
When organizations pay attention to each of the stages in the development of products or services they offer, their quality is just better. Improvement systems allow to to correct failures along the way and wave obstacles that prevent the company from growing properly.
How can you identify a good continuous improvement program?
Continuous improvement plans can look different for each organization. Everything will depend on the nature of each business, as well as its products, services, and processes.
However, for a continuous improvement plan to be successful, it must be tailored for the specific needs of each company. A company that needs to carry food from one point to another does not have the same problems as a company focused on the import and export of auto parts.
Hence, a good continuous improvement program mimics the areas of opportunity of each company and its business objectives, generating ideas on the most viable solutions, executing, measuring, and optimizing them. George T. Doran introduced in 1981 the acronym S.M.A.R.T (specific, measurable, assignable, realistic and time-related) as a guide in the setting of goals and objectives for better results.
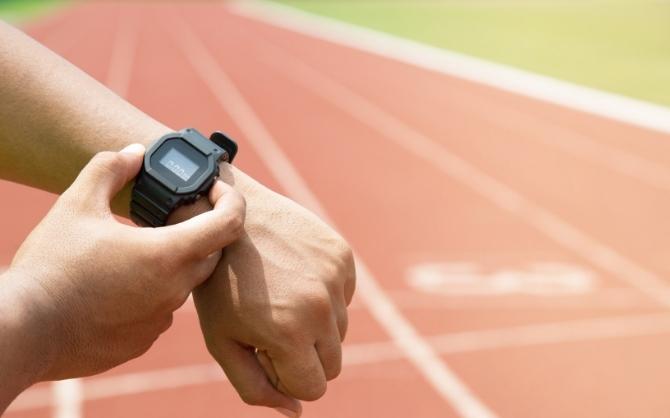
S.M.A.R.T (specific, measurable, assignable, realistic and time-related)
Who is in charge of developing plans for ongoing improvement?
You might believe that implementing a continuous improvement program should be done on a broad scale. However, the reality is that a good improvement plan depends entirely on the participation of employees and their level of involvement. It doesn’t matter if we are talking of a small group or an entire army.
Project managers or business owners are usually the superheroes of this story. They are the ones in charge of these type of programs. Large firms can streamline their operations in a relatively short amount of time with tremendous benefits by combining this tiny but consistent effort with senior management leadership.
Now comes the question, should companies hire an external partner to enforce such programs? Or should they handle it in-house with their current staff? Both solutions are viable, but pretty often hiring an external company can help incorporating different point of views to solve a well-known problem.
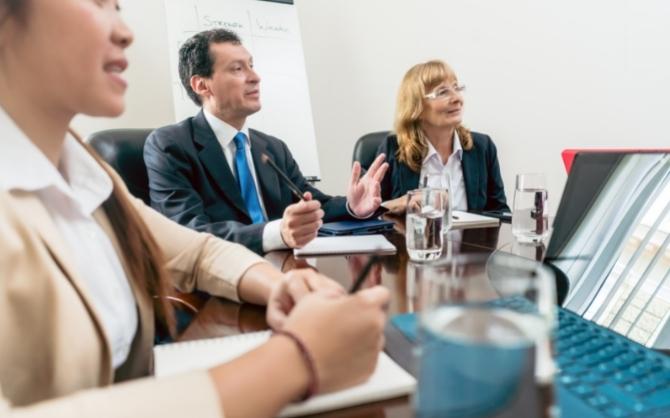
Senior Managers are usually in charge of leading continuous improvement programs.
5 Reasons why you should implement a continuous improvement plan in your company today!
Although it is true that the continuous improvement plan for each project varies greatly according to the needs of each organization, the benefits of achieving operational excellence will be the same in most cases:
1. Continual improvement allows process optimization
A well-structured continuous improvement plan makes key processes within the entire organization a lot more efficient. This way you will be able to identify affected procedures and on the other hand, reward the ongoing effort with quick wins.
Periodic self-evaluations of the parties concerned should be carried out for this purpose in order to identify pain points and establish improvement initiatives. The idea is to make tiny changes that will save the organization money in the long run.
2. Better offer
Self-analysis helps to improve the quality of products and services. It also helps senior leadership to better understand consumer wants and needs, and find options to create loyalty strategies, improving brand reputation and customer satisfaction.
3. Internal communication
A continuous improvement program paves the way in which internal changes, approaches, and company objectives are communicated to employees. In order to obtain the desired outcome, employees involvement is a must. They are the ones who will make the continuous improvement program a success or a failure.
A correct execution allows finding ways to contribute to the individual growth of each employee, and at the same time meet the business goals.
4. Improves the organizational climate
When the company’s teams work in harmony, employee performance is much better and more efficient. Recent studies show that when employees feel supported by their team, and understand the strengths of each member; they form a better team.
Continuous improvement efforts promote this motivation in employees, always looking for ways to improve the environment in which they work.
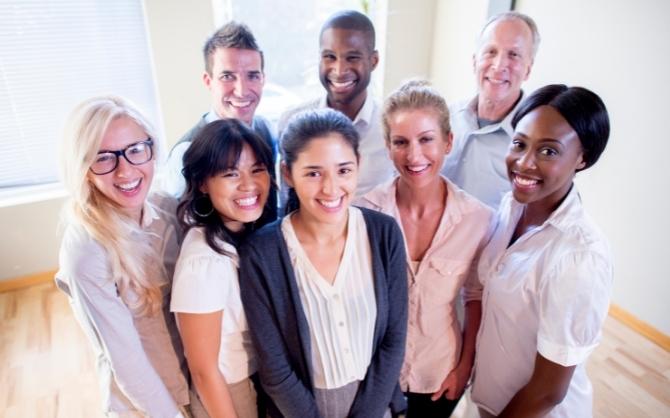
Continuous improvement efforts promote employees motivation
5. Boosts productivity
The goal of improvement plans is to optimize day-to-day efficiency within companies, which in turn leads to improved tasks and delivery times for employees.
The fact that human talent is aware of the constant search by their leaders to improve their quality of work life, helps them to perform their daily tasks with more motivation, creating clearer and more efficient work processes, to avoid double work and burnout.
What are the 4 components of continuous improvement?
Although it is true that there are different models of continuous improvement, in all of them there are 4 constants that serve as the pillars for a continuous improvement program to provide the expected results: plan, execute, verify and act.
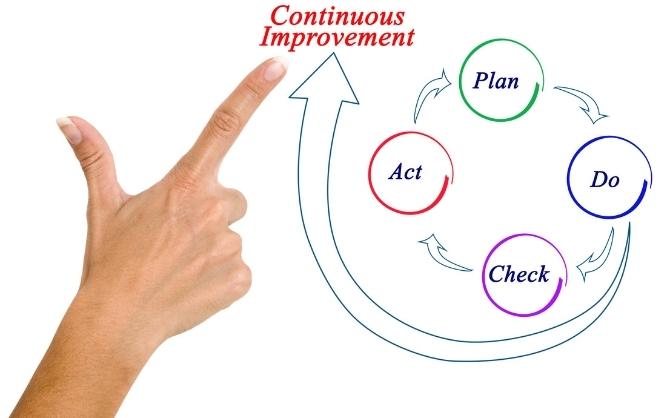
The 4 pilars of continuous improvement: Plan, Do, Check, Act
Plan
In this step, the general panorama of the organization’s activities susceptible to improvement is identified and the objectives to be achieved in this respect are set.
The search for improvement opportunities can be carried out with the participation of working groups, listening to the opinions of the workers, and searching for new technologies, among other procedures.
Execute
The changes that are considered necessary to make the improvements are executed, applying a small-scale pilot test to determine the operation before making large-scale changes.
Verify
Once the improvement has been made, a test period is carried out to verify its proper functioning in the area where the pilot was carried out; if the improvement does not meet the initial expectations, modifications are made to adjust to the expected objectives.
Act
Finally, after the test period, the results are studied and compared with the performance of the activities before the changes were done. It is also critical to consider customer feedback at this stage.
If the results are satisfactory, the improvement will be implemented definitively and on a large scale in the organization; but if the desired result is not obtained, it will be necessary to evaluate if changes will be made or if the improvement will be discarded.
After the fourth phase is accomplished, the first step is revisited to research new ideas and improvement areas.
The 4 pilars of continuous improvement: Plan, Do, Check, Act
Continuous improvement models
Among the most popular continuous improvement models used by businesses, the following stand out:
The Shewhart Cycle
In this organizational model, the 4 fundamental steps of continuous improvement are applied as they are: plan, do, check, and act.
It is a cycle that is part of a cybernetic control in a production environment and lends itself to 3P total quality management.
The Kaizen Philosophy
This is a Japanese method that promotes a culture of continuous improvement through the elimination of what does not work in the current processes of a business, aiming to improve efficiency.
The idea of this method is to be able to identify and propose solutions in all areas of the business, through small efforts that will help the organization to achieve its objectives, improving the experience of customers and employees.
To implement this methodology, the following steps must be followed:
- Selection of the theme: a theme should be chosen that is aligned with the fulfillment of the company’s objectives. For example, decreasing production costs, improving quality, optimizing production processes, improving the user experience, etc.
- Work team selection: the idea is to find the people who will be in charge of the different work areas that will help to carry out the improvement. The idea of incorporating human talent from different departments in the team is that each one generates a contribution from his or her point of view.
- Information analysis: once the processes and what happens within the areas to be improved are understood, the data must be analyzed, so that based on the results the corresponding actions can be taken in the continuous improvement of the processes.
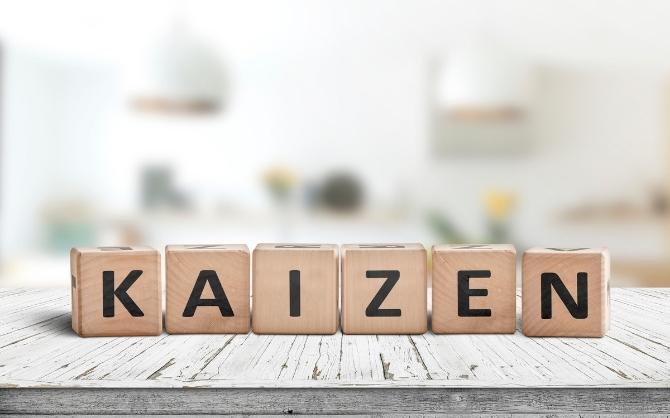
Kaizen focuses on eliminating waste, improving productivity, and achieving sustained continual improvement in targeted activities and processes of an organization.
5S Method
This is a technique for labor management based on 5 principles, and its main objective is to organize and give meaning to the functions, improving the productivity of the teams without intervening in costs.
As an interesting fact, it was the Toyota corporation that popularized these practices in the 1960s, as its main goal was to create a better-structured workplace using these principles:
- Qualification: the workstation is analyzed and everything that does not fulfill a necessary function for performance is eliminated, in such a way that it seeks to clean and qualify tools and documents, freeing up space in every way.
- Organization: an orderly space allows a more efficient performance, having always at hand the elements that are mostly occupied. This saves a lot of time when it comes to finding the tools for daily use.
- Cleanliness: a clean and tidy workspace helps to avoid accidents and distractions. What can be eliminated, should be eliminated, to avoid the accumulation of unnecessary objects in the workplace.
- Standardization: looks for anomalies in the workplace. If the three previous functions are fully complied with, it will be easier to identify these faults. The objective is to standardize processes as optimally as possible.
- Discipline: each factor involved complements the previous one; discipline allows to achieve the desired objectives while maintaining the motivation of the team, since the objectives are clear, reaching the planned goals in the shortest time.
Lean Manufacturing
Implemented in the 1940s in Toyota’s production plants in Japan, this work philosophy seeks to identify and eliminate all activities that do not add value within a company but do add cost and time.
Similarly, this methodology of continuous improvement is opposed to the American ideologies related to mass production and seeks to find an efficient solution to the amount of waste generated in each production.
The success of this powerful technique focuses on being able to identify, on a continuous basis, all the opportunities for improvement that are hidden in the work processes, in order to find all the details that can damage and make the work of the teams less efficient.
Kanban
This continuous improvement method seeks to streamline work functions by dividing them into phases by means of “visual cards”.
Each visual card should indicate all the information necessary for the team to understand what actions are to be carried out, i.e., the task, function, and observations are described as follows:
– Effective visualization of tasks
– Management processes based on clear objectives
– Prioritization according to urgency and importance
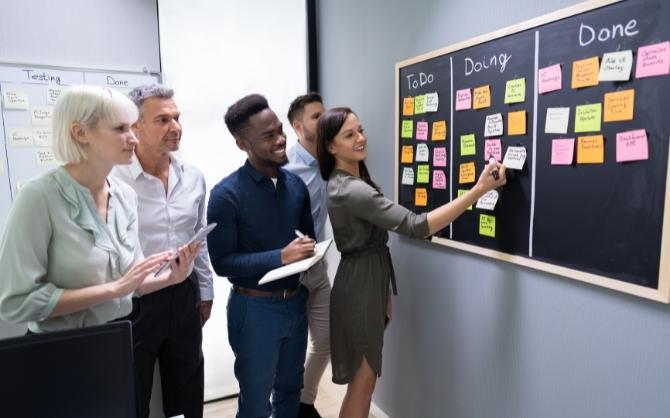
Kanban boards use cards to represent work items and columns to represent each stage of the process to visually depict work at various stages of a process.
Poka Yoke
This is a technique that seeks to eliminate errors in the quality area from the current state, in order to continue implementing continuous improvement systems in the company, taking control of the production system for improvement, and eliminating unnecessary costs and processes.
The key lies in detecting errors and taking immediate action, as in factory processes, for example, where the aim is to establish indicators that are easy to remember, such as colors or shapes, in order to remember the processes more clearly and easily and avoid making a mistake.
Six Sigma
Generated in the 80s by Motorola engineers, this continuous improvement process was created with the purpose of reducing variability and failures in the delivery of products or services to the customer.
Statistically speaking, it is an equation that allows measuring, analyzing, implementing, and controlling processes to improve results, reaching a degree of efficiency of 99.99%.
This means that, for every million units, only 3.4 of the products will come out with a defect or outside the agreed parameters.
The 5 Why’s
The approach of this methodology is based on locating the root causes of the recognized problems within the organization.
In order to identify these causes, this methodology proposes to ask up to 5 “Why?” questions, since the answer to each of these questions will lead to the generation of the next question until the initial problem is located.
Performing this technique allows us to see in perspective the strong impact that a small error can have and how it can affect the whole process.
On many occasions, this method shows us that not every problem has a linear path, but can be derived and affect several areas.
Examples of the continuous improvement program
There are several examples of continuous improvement that have been implemented by many companies over the last few years.
Some of the most interesting and most successful are the following:
ISO Standard
This is one of the most successful examples of continuous improvement, since thanks to ISO standards, quality standards are applied at the international level.
This allows the production of standardized products that comply with a series of norms and requirements, which ensure their good quality and compliance with the functions for which they have been designed.
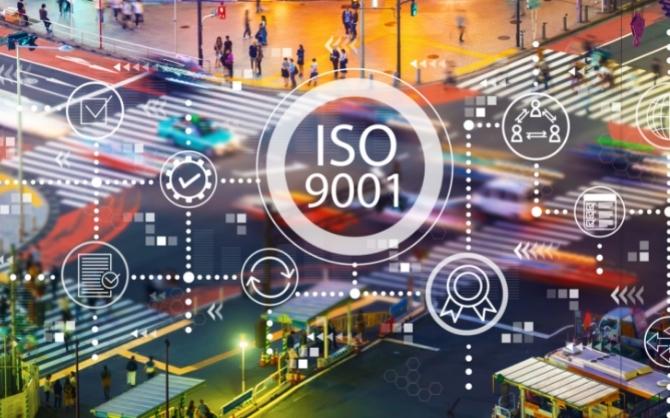
Think of ISO standards as a formula that describes the best way of doing something.
Environmental Assessment Systems
The environmental assessment systems control all aspects related to the manufacture of the products, allowing complete control over the final products and their impact on the environment.
Thanks to the continuous improvement procedures in environmental assessment systems, it is possible to deal with mass production in a more holistic way.
Quality Management Systems
Consists of the implementation of systems aimed at verifying final satisfaction.
It is thanks to these systems that various companies can obtain information that can then be applied to improve those aspects that do not provide complete satisfaction, allowing the final customer experience to be continuously improved.
Process Management System
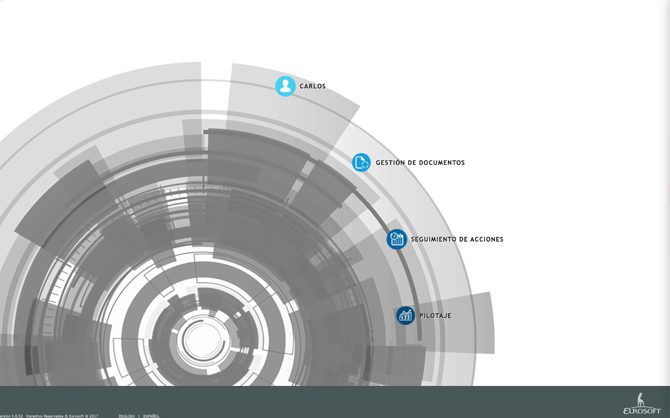
Eurosoft System at ILS
It is a work methodology used to control the modeling, visibility, and management of the company’s production, support and business processes.
The objective is to align processes with an organization’s strategic goals, design and implement process architectures, and establish process measurement systems.
At The ILS Company, we have this methodology, through which we have greater visibility and monitoring not only of the processes, but also of the resolution of non-conformities, risk analysis, and internal audits of the quality system.
It is very important to consider that a continuous improvement plan never ends. In many organizations, there are even teams that specialize in these services. The important thing in this process is to keep in mind that there is always room for improvement, so stay focused.